新型气动马达的研究
2017-09-18 来自: 浙江新汕自控阀门有限公司 浏览次数:969
气动元件作为控制系统执行元件,受到了人们的关注。现在就一种新的气动叶片式马达的结构进行理论探讨,为提高气动马达效率、节能降耗的目的提供一种新的设计思路。
与目前使用的传统型的叶片式气动马达相比,“双弧双缸组合式”气动马达在缸体外部尺寸不变的情况下,由于有效增大了缸体进气腔体积,因此有效提高了马达的转速并改善了进气方向,有效降低了进气噪音,为提高气动马达效率、节能降耗,提供了一种新的设计方案。
1、“双弧双缸组合式”气动马达设计理论与方法
气动工具以其高效率、高转速、大力矩、无电磁辐射、安全性能高、适于流水化作业等特点,目前在工具类产品中占有较大市场,有的还用于特殊的工作环境。有关它的分析研究理论也已很多, 现就一种曾获得专利的(专利号:ZL00222701. 0)“双弧双缸组合式”气动马达,作一理论分析。
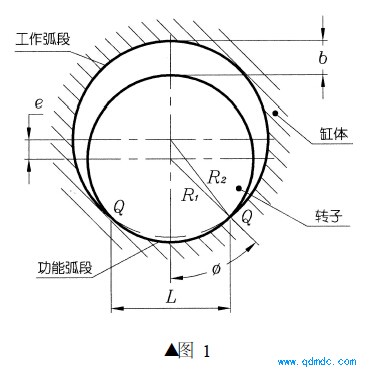
该“双弧组合式”气动马达其转子与缸体其配合关系如图1。可建立几何关系为:
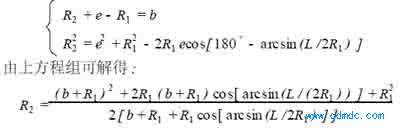
从图1可看出,缸体有两个突变点Q, 即工作弧段与功能弧段的交点。这两处突变点对叶片的冲击力很大,使叶片的寿命大为缩短。为解决该问题采用“双弧双缸组合式”结构,见下图2缸体整体结构:
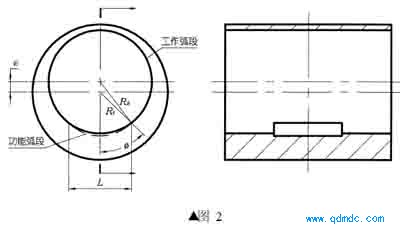
缸体由圆柱腔体和中部带凹槽的台阶腔体组成,凹槽将圆柱腔体分成两半(即两侧为360°范围内的工作弧段) , 圆柱腔体形成叶片的工作弧段,凹腔为功能弧段,故称“双弧双缸组合式”结构。该结构由于叶片在360°范围内始终在圆柱腔体旋转,未扫掠功能弧段,故有效避免了冲击突变点Q。
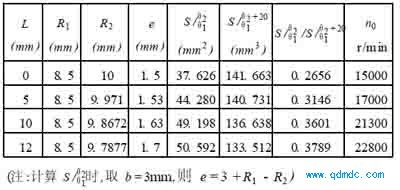
从上表数据可看出,若取L = 10作为马达结构设计尺寸, 则在保持马达长度与外径(即马达整体尺寸)不变的情况下,转速比传统结构提高了( 21300 - 15000) /15000 = 42%。因驱动力矩Mf =mw2 fR2 (R2 - a) ,所以驱动力矩比传统结构增大了92. 68%。显然从理论上分析该马达结构比传统马达结构的驱动性能有显著的提高。以上在局部计算时可能存在一定误差,特别是修正系数K值随设计方案L的取值不同有一
定的差异,它的取值范围为L = 0. 18~0. 3,通过分析可看到了一个必然因素,那就是V1 的增大和R2 的减小必然会产生转速和驱动力矩的明显增大。
2、马达的结构特点
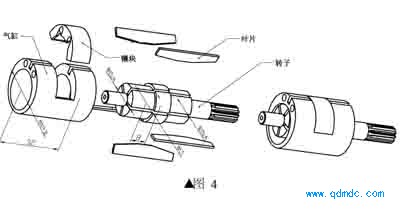
该马达整体结构如图4 (取L = 10的设计方案) :
从图4中可看出,该气动马达转子中部有一圆柱形凸台,与传统型的单一圆柱形不同,缸体有一个为实现“功能弧段”作用而设计的弧形结构镶块。弧形结构镶块使叶片不产生磨擦,对转子凸台起密封的作用。所以为了有良好的跑合性,该镶块材料宜采用锡基粉末冶金。该结构对叶片侧面耐磨性、抗剪性有一定要求,在当今粉末冶金技术已很成熟的状况下,若转子采用铁基等粉末冶金可以非常有效的提高叶片的耐磨寿命,叶片也可采用抗剪性较强的复合材料。
3、气动马达马达结构的优缺点
311 优点
(1) 缸体外部尺寸与进气压力不变的情况下,有效提高了马达的转速, 提高了输出力矩, 提高了效率, 节约了能源。
(2) 由于输出力矩的增大,按表中L = 10一栏参数设计时,旋转力矩理论上可增加两档位,即:如果原为M2~M4可增至为M2~M6。
(3) 图4“双弧双缸组合式”结构中,其镶块的进气孔与排气孔开孔方向与位置,可使进气与排气的方向与叶片旋转方向基本一致,与传统进气与排气的方向与叶片旋转方向成90°相比较可有效降低噪声。
312 缺点
(1) 加工工艺性比传统复杂,但当今的数控加工技术是完全能保证的,对于普通设备使用“靠模”也能保证其加工
精度。
(2) 尚需要对马达部分锡基粉末冶金镶块进行旋转跑合过程:从马达转子的输出端加电机进行驱动,同时去掉消音罩,并在进气口接上适当的气压(不能过高,约0. 2~0. 3Mpa) ,可将磨合后的粉末吹尽。然后再进行超越离合器的组装。